
Eurobend offers the most comprehensive range of rebar processing and welding equipment covering every precast application. Our portfolio of more than 100 machine types includes fully automated and electronically controlled machines for the straightening, cutting and bending of all types of steel wire and rebar and mesh welding machines for the production of standard and special construction and fencing mesh, as well as and precast reinforcing elements.
Elematic, in turn, has the industry’s widest portfolio of precast manufacturing solutions including plants, production lines, single machines, the related services and knowledge network that covers all aspects of precast concrete in buildings – manufacturing as well as the method and the design.
Similar product philosophy:
The two companies have a similar product philosophy and, therefore, products that match very well together. Eurobend’s system is modular, and the degree of automation in the machinery can be increased by adding more modules to the machines. Elematic has a very similar approach.
“We have packaged our precast production line offering into three technology levels – Semi, Pro and Edge - where capacity and automation levels differ. Together with Eurobend we can offer automation levels that best meet the needs of a particular precast factory, says Lassi Järvinen, Technical Director at Elematic. The most basic technology level ensures that getting started with precast production is easy. In time, if more capacity is required, the level of automation can be increased.
The equipment that Elematic and Eurobend offer together is a strong combination for a successful precast operation, regardless of the size and geographic location of the company.
”We are pleased to have Eurobend as our cooperation partner. They are a very innovative developer of rebar processing and welding machinery lines with a portfolio that perfectly fits for our precast production lines” says Mats Jungar, CEO of Elematic.
Top quality guaranteed:
The collaboration between Elematic and Eurobend serves as a quality guarantee to precasters worldwide. They will receive the best precast production solutions combined with the most innovative and technologically advanced rebar processing and welding machinery lines.
“Elematic is one of the top brands in the precast field worldwide. Their expertise and quality product lines are the perfect match to our innovative equipment. Basically, we provide what the market has been looking for: a synergy between the two leading manufacturers in the precast and construction business sector,” says Isabel Protopapa, Managing Director of Eurobend.
“Precast is one of the most – if not the most – demanding area of the construction business. To be successful, you need to provide excellent quality and craftsmanship together with reliable, trouble-free operation. We strongly believe that the cooperation between Elematic and Eurobend will provide all that to every precast operation, regardless of size, region or continent,” says Anthony Anagnos, President of Eurobend.
THE SYNERGY BETWEEN ELEMATIC & EUROBEND OFFERS THE FOLLOWING SOLUTIONS:
SEMI LEVEL:
Elematic SEMI technology level plant is an easy startup of precast production with a low investment. It is perfect for precast pioneers, precasters who only need a few products or builders who need production for just one particular project.
EUROBEND’S machines that accompany the SEMI version include:
Elematic, in turn, has the industry’s widest portfolio of precast manufacturing solutions including plants, production lines, single machines, the related services and knowledge network that covers all aspects of precast concrete in buildings – manufacturing as well as the method and the design.
Similar product philosophy:
The two companies have a similar product philosophy and, therefore, products that match very well together. Eurobend’s system is modular, and the degree of automation in the machinery can be increased by adding more modules to the machines. Elematic has a very similar approach.
“We have packaged our precast production line offering into three technology levels – Semi, Pro and Edge - where capacity and automation levels differ. Together with Eurobend we can offer automation levels that best meet the needs of a particular precast factory, says Lassi Järvinen, Technical Director at Elematic. The most basic technology level ensures that getting started with precast production is easy. In time, if more capacity is required, the level of automation can be increased.
The equipment that Elematic and Eurobend offer together is a strong combination for a successful precast operation, regardless of the size and geographic location of the company.
”We are pleased to have Eurobend as our cooperation partner. They are a very innovative developer of rebar processing and welding machinery lines with a portfolio that perfectly fits for our precast production lines” says Mats Jungar, CEO of Elematic.
Top quality guaranteed:
The collaboration between Elematic and Eurobend serves as a quality guarantee to precasters worldwide. They will receive the best precast production solutions combined with the most innovative and technologically advanced rebar processing and welding machinery lines.
“Elematic is one of the top brands in the precast field worldwide. Their expertise and quality product lines are the perfect match to our innovative equipment. Basically, we provide what the market has been looking for: a synergy between the two leading manufacturers in the precast and construction business sector,” says Isabel Protopapa, Managing Director of Eurobend.
“Precast is one of the most – if not the most – demanding area of the construction business. To be successful, you need to provide excellent quality and craftsmanship together with reliable, trouble-free operation. We strongly believe that the cooperation between Elematic and Eurobend will provide all that to every precast operation, regardless of size, region or continent,” says Anthony Anagnos, President of Eurobend.
THE SYNERGY BETWEEN ELEMATIC & EUROBEND OFFERS THE FOLLOWING SOLUTIONS:
SEMI LEVEL:
Elematic SEMI technology level plant is an easy startup of precast production with a low investment. It is perfect for precast pioneers, precasters who only need a few products or builders who need production for just one particular project.
EUROBEND’S machines that accompany the SEMI version include:
- An entry level straight bar fed flexible mesh welding line with a servo-driven multi point automatically moving welding head, type PL XY
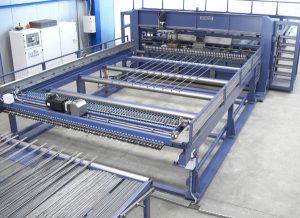
- Either a single-line (type MELC MONO-LINE) or flexible multi-line (Type MELC FLEXI-LINE) rotor straightening and cutting machine (which offers automatic diameter changeover in 2-3 seconds due to our patented rebar feeding convergence system) equipped with up to six rotors/lines.
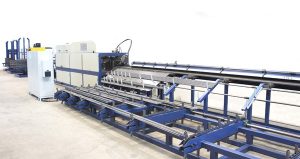
- An entry level rebar bending machine (type G-STAR ECO) capable of producing efficiently and accurately two-dimensional stirrups and various types of rebar forms.
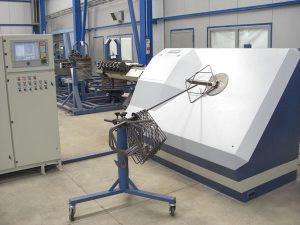
PRO LEVEL:
Elematic PRO production lines and machines are especially designed for producing different types of precast products with medium capacity.
For this mid-range solution, EUROBEND suggests:
Elematic PRO production lines and machines are especially designed for producing different types of precast products with medium capacity.
For this mid-range solution, EUROBEND suggests:
- An increased capacity straight-bar-fed flexible mesh welding line with two servo-driven multi-point automatically moving welding heads (type PL X-Y) processing straight wires/bars, or a fully automatic, coil-fed machine version (type PL X-Y AMM) offering automatic feeding of different diameters for the cross and line wires as well as feeding of different lengths in the same mesh, offering also the capability to produce mesh with openings.
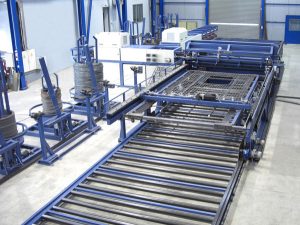
- A flexible multi-line rotor straightening and cutting machine (type MELC FLEXI-LINE) rotor straightening and cutting machine (which offers automatic diameter changeover in 2-3 seconds due to our patented rebar feeding convergence system) equipped with up to six rotors/lines.
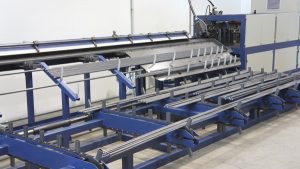
- An advanced rebar bender (type G-STAR SE) featuring powered straightening rollers, for a precise and evenly distributed feed force without re-bar marking, automatic roller adjustment and re-bar diameter changer, adjustable counter-torsion system (patented) always producing flat shapes regardless of re-bar quality, axial twist and bending direction.
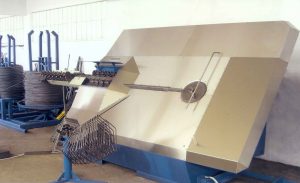
- A shear line (type BC) for processing larger diameters of straight bars. Processing up to 10 re-bars simultaneously, with fast and easy re-bar loading into the measuring and feeding channel, automatic feeding, measuring, cutting and separation of the processed re-bars and automatically aligning rebar mechanism.
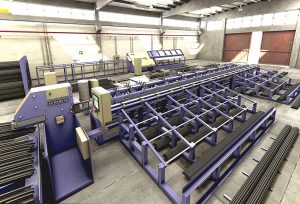
EDGE:
Elematic EDGE production lines and machines are especially designed for precasters seeking very high capacity, a wide product range, and highly automated precast production.
This high capacity production line will require:
Elematic EDGE production lines and machines are especially designed for precasters seeking very high capacity, a wide product range, and highly automated precast production.
This high capacity production line will require:
- A fully automatic, coil-fed machine version (type PL X-Y AMM) offering automatic feeding of different diameters for the cross and line wires as well as feeding of different lengths in the same mesh., or a high output PLC AMM Series, which is a coil fed machine that covers every application in the production of engineering, construction, customized mesh and mesh with openings for prefabricated concrete elements. Eliminates all idle times and at least doubles productivity in comparison to conventional welding lines. Offering automatic no downtime when changing: Wire coils-Wire diameters- Wire spacing-Mesh dimensions.
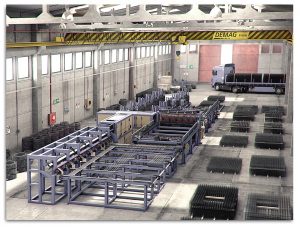
- A flexible multi-line rotor straightening and cutting machine (type MELC FLEXI-LINE) rotor straightening and cutting machine (which offers automatic diameter changeover in 2-3 seconds due to our patented rebar feeding convergence system) equipped with up to six rotors/lines.
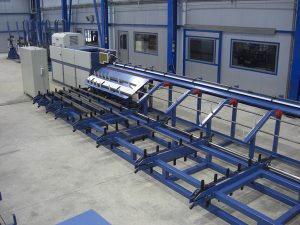
- An advanced rebar bender (type G-STAR SE or G-STAR SE TRIS, producing also three-dimensional stirrups) featuring powered straightening rollers, for a precise and evenly distributed feed force without re-bar marking, automatic roller adjustment and re-bar size changer, adjustable counter-torsion system (patented) always producing flat shapes regardless of re-bar quality, axial twist and bending direction.
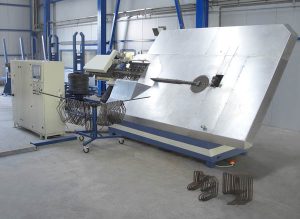
- A shear line (type BC) for processing larger diameters of straight bars. Processing up to 10 re-bars simultaneously, with fast and easy re-bar loading into the measuring and feeding channel, automatic feeding, measuring, cutting and separation of the processed re-bars and automatically aligning rebar mechanism.
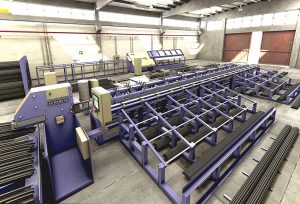